Carbon steel bolts are among the most commonly used fasteners across a wide range of industries, from construction and infrastructure to automotive, machinery, and even household applications. Known for their strength, durability, and affordability, carbon steel bolts serve as a critical component in countless structural and mechanical systems. But what exactly makes carbon steel bolts such a popular choice? This comprehensive guide will explore their characteristics, classifications, benefits, limitations, manufacturing processes, and common applications to give you a complete understanding of these essential fasteners.
Carbon steel bolts are fasteners made primarily from carbon steel, a type of steel that contains varying levels of carbon (generally up to 2.1% by weight) and small amounts of other elements such as manganese, phosphorus, and sulfur. The carbon content significantly influences the bolt’s mechanical properties, such as hardness, tensile strength, and ductility. These bolts are typically used to connect materials together—either temporarily or permanently—and are known for their robustness and reliability.
Carbon steel bolts can be manufactured in different grades and hardness levels, depending on the percentage of carbon and the heat treatment applied. They are available in various head shapes, thread types, sizes, and coatings, making them suitable for a wide range of purposes.
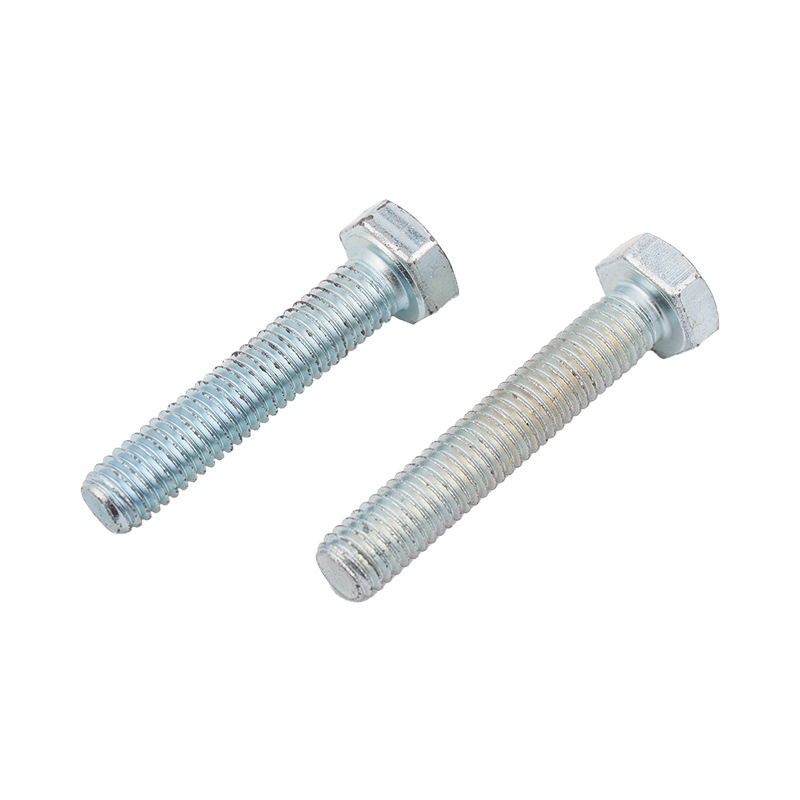
Primary Characteristics of Carbon Steel Bolts
1. Mechanical Strength
Carbon steel bolts offer high tensile and yield strength, which makes them ideal for structural and load-bearing applications. The strength of the bolt can vary significantly depending on the grade of carbon steel used:
Low Carbon Steel Bolts (up to 0.25% C): More ductile and malleable, but lower strength.
Medium Carbon Steel Bolts (0.25%–0.60% C): Good balance between strength and ductility.
High Carbon Steel Bolts (0.60%–1.00% C): Very high strength and hardness, but less ductile and more brittle.
2. Hardness and Wear Resistance
As the carbon content increases, so does the hardness of the bolt. High-carbon steel bolts exhibit excellent wear resistance, making them suitable for applications subject to friction and mechanical stress.
3. Tensile Properties
Carbon steel bolts are engineered to endure heavy tensile loads without deforming. High-strength bolts can achieve tensile strengths upwards of 100,000 psi (pounds per square inch), depending on the grade and heat treatment.
4. Ductility and Toughness
Low and medium carbon steel bolts provide good ductility and toughness, which allows them to absorb shock and vibrations without fracturing. This is crucial in applications such as bridge construction or heavy machinery.
5. Corrosion Resistance (With Coating)
Carbon steel in its raw form is not particularly corrosion-resistant. However, most carbon steel bolts are treated or coated to protect them from environmental elements. Common coatings include:
Zinc plating
Hot-dip galvanizing
Black oxide finish
Phosphate coating
Each coating offers varying degrees of protection against moisture, chemicals, and atmospheric conditions.
Grades and Standards of Carbon Steel Bolts
Carbon steel bolts are available in several grades, as defined by different international standards. Some common ones include:
ASTM Standards (U.S.)
ASTM A307: Low carbon steel bolts for general use.
ASTM A325 / A490: High-strength bolts used in structural applications.
SAE Grades
Grade 2: Low or medium carbon steel, used for light-duty applications.
Grade 5: Medium carbon steel, quenched and tempered; moderate strength.
Grade 8: High carbon steel, quenched and tempered; high strength.
ISO/Metric Grades
Class 4.6, 8.8, 10.9, 12.9: Metric bolts with increasing levels of strength and hardness.
Advantages of Carbon Steel Bolts
Carbon steel bolts offer a range of benefits that make them attractive for both manufacturers and end users:
Feature |
Benefit |
High Strength |
Supports heavy loads and structural integrity |
Cost-Effective |
Affordable compared to stainless steel or specialty alloys |
Versatile |
Available in many sizes, thread types, and finishes |
Good Machinability |
Easy to fabricate, cut, and thread |
Heat Treatable |
Properties like hardness and tensile strength can be enhanced through heat treatment |
Widely Available |
Easily sourced from global suppliers |
Limitations and Considerations
While carbon steel bolts are versatile and reliable, they do come with a few limitations:
Low Corrosion Resistance: Without proper coating, carbon steel rusts easily, especially in marine or humid environments.
Brittleness at High Carbon Levels: High carbon content improves hardness but can reduce flexibility, increasing the risk of fracture under impact or dynamic loads.
Not Ideal for High-Temperature Applications: Carbon steel may lose strength and oxidize at elevated temperatures unless specifically alloyed.
Common Applications of Carbon Steel Bolts
Given their strength and affordability, carbon steel bolts are used in a variety of sectors:
1. Construction and Infrastructure
Steel frames and structural beams
Bridges and tunnels
Roofing and trusses
2. Automotive and Transportation
Engine and suspension assemblies
Axles, brakes, and drive shafts
Railroads and heavy trucks
3. Industrial Machinery
Presses, pumps, and compressors
Conveyor systems
Factory equipment and tools
4. Energy and Utilities
Power plant installations
Wind and solar panel mounts
Pipelines and refineries
5. General Manufacturing and DIY
Home appliances
Furniture assembly
Agricultural tools
Manufacturing Process of Carbon Steel Bolts
Carbon steel bolts go through a rigorous production process to achieve their final form:
Wire Rod Preparation: Raw steel is processed into wire rods of the required diameter.
Cold Heading or Hot Forging: Bolt heads are formed using mechanical or thermal processes.
Thread Rolling: Threads are created by rolling dies under high pressure.
Heat Treatment (if required): To enhance strength and hardness.
Surface Finishing: Protective coatings or platings are applied.
Inspection and Quality Control: Bolts are checked for dimensions, strength, and performance before packaging.
Maintenance and Best Practices
To extend the life of carbon steel bolts and prevent premature failure, it is important to follow good maintenance practices:
Use Protective Coatings: Always select bolts with corrosion-resistant finishes for outdoor or chemical environments.
Torque Correctly: Avoid under- or over-tightening, which can weaken the joint.
Regular Inspection: Especially in high-vibration or load-bearing applications, inspect bolts periodically for signs of wear, rust, or loosening.
Storage: Store in dry environments to prevent oxidation and corrosion during warehousing.
Conclusion
Carbon steel bolts are an essential component in modern engineering and manufacturing. Their high strength, cost-effectiveness, and adaptability make them a go-to fastener solution for countless applications. Understanding their characteristics—such as tensile strength, hardness, ductility, and coating options—enables better selection for specific uses and environments.
While they may not be the best fit for every condition, particularly those involving high corrosion or extreme temperatures, proper material selection and protective treatments can significantly enhance their performance. With the right knowledge and maintenance, carbon steel bolts can offer long-lasting, secure, and economical fastening solutions across industries.