Carbon steel nuts are widely valued in various industries for their mechanical strength, affordability, and ease of manufacture. However, one notable limitation of carbon steel is its inherent susceptibility to corrosion. Unlike stainless steel, which contains chromium and other alloying elements that form a passive protective oxide layer, carbon steel lacks these natural corrosion-resistant properties. As a result, carbon steel nuts can experience oxidation and rust when exposed to moisture, chemicals, or harsh environmental conditions.
Corrosion Resistance Characteristics of Carbon Steel Nuts
1. Prone to Oxidation and Rust Formation
When carbon steel nuts come into contact with water and oxygen, a chemical reaction occurs leading to the formation of iron oxide or rust. This rust is a porous, flaky substance that does not protect the underlying metal but instead accelerates further corrosion. Over time, rust can cause weakening, pitting, and eventual failure of the fastener, compromising the integrity of mechanical assemblies.
2. Environmental Sensitivity
The rate and severity of corrosion depend heavily on the surrounding environment:
Humidity and Moisture: In humid or wet conditions, especially outdoors, the likelihood of corrosion is high. Frequent exposure to rain, condensation, or water splashes creates an environment conducive to rust.
Salt and Chlorides: Environments near the sea or in areas where deicing salts are used pose an elevated corrosion risk due to the chloride ions that aggressively attack steel surfaces.
Industrial Pollutants: Acidic gases like sulfur dioxide or nitrogen oxides in industrial or urban areas can accelerate corrosion by forming acidic moisture on metal surfaces.
Temperature Fluctuations: Repeated cycles of heating and cooling can cause condensation, leading to moisture accumulation and corrosion. High temperatures combined with corrosive chemicals can further exacerbate deterioration.
3. Lack of Passive Protective Layer
Unlike stainless steel, which forms a stable, chromium-rich oxide layer that protects the metal from further corrosion, carbon steel does not have such a self-healing barrier. This lack means that any damage to the surface coating or finish can expose bare steel, making the nut vulnerable to rapid corrosion.
Methods to Enhance Corrosion Resistance of Carbon Steel Nuts
To counter the natural corrosion vulnerability, manufacturers apply various surface treatments and coatings to carbon steel nuts. These protective layers serve as physical barriers, sacrificial coatings, or chemical passivation layers, significantly enhancing corrosion resistance and extending service life.
1. Zinc Coating (Galvanization)
Electroplated Zinc: A thin layer of zinc is electroplated onto the surface of the nut, providing sacrificial protection. Zinc corrodes preferentially, protecting the steel underneath even if the coating is scratched.
Hot-Dip Galvanizing: Involves immersing the nuts in molten zinc, resulting in a thicker, more durable coating ideal for harsh outdoor and industrial environments. This process creates a metallurgical bond between zinc and steel, enhancing resistance against abrasion and corrosion.
Zinc coatings are popular for their cost-effectiveness and reliability, especially in construction, automotive, and infrastructure projects.
2. Black Oxide Finish
Black oxide is a chemical conversion coating that forms a thin layer of magnetite (Fe3O4) on the surface. It provides mild corrosion resistance and reduces light reflection, improving aesthetics.
Usually combined with oil or wax coatings to improve corrosion protection, black oxide is often used in indoor or dry environments.
3. Phosphate Coating
This treatment creates a crystalline phosphate layer that enhances corrosion resistance and improves adhesion of subsequent coatings like paint or oil.
Often used in automotive and machinery applications, phosphate coatings also provide some lubrication benefits during assembly.
4. Powder Coating and Paints
Powder coatings and industrial paints offer a robust, non-metallic protective barrier against moisture and chemicals.
These coatings can be customized for color and texture, improving both corrosion protection and visual appeal.
5. Cadmium Plating
Although cadmium plating offers excellent corrosion resistance, especially in marine environments, it is less favored today due to environmental and health concerns associated with cadmium toxicity.
6. Other Protective Treatments
Electropolishing and passivation—more common with stainless steel—can also be applied to carbon steel to smooth surfaces and reduce corrosion initiation sites.
Corrosion inhibitors may be applied as sprays or oils to protect nuts during storage or temporary exposure.
Additional Factors Affecting Corrosion Resistance
Thread Compatibility and Galvanic Corrosion: When carbon steel nuts are paired with bolts made from different metals (e.g., stainless steel), galvanic corrosion can occur due to electrochemical differences. Proper material pairing or insulating coatings help mitigate this issue.
Environmental Control: In some applications, controlling humidity, temperature, or exposure to corrosive agents (e.g., using sealed enclosures) can improve nut lifespan.
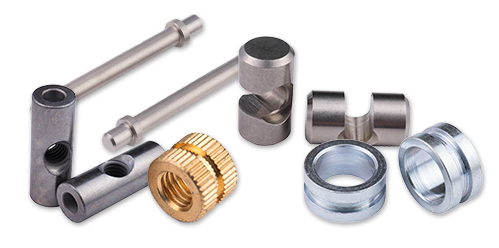
Summary
While carbon steel nuts inherently have limited corrosion resistance, applying surface treatments such as zinc plating, hot-dip galvanizing, black oxide coatings, phosphate treatments, and powder coatings significantly improves their durability against rust and environmental damage. The choice of treatment depends on the intended application, exposure conditions, cost constraints, and regulatory requirements. With proper coating and maintenance, carbon steel nuts can reliably serve in demanding industrial, construction, automotive, and manufacturing settings, combining strength with enhanced corrosion protection to maximize service life and safety.