In modern manufacturing, where lightweight structures, space efficiency, and reliability are crucial, traditional fastening methods like welding, soldering, or tapping threads often fall short. In such cases, pressure rivet screws—also known as self-clinching screws—serve as a vital solution for joining components, especially in thin-walled sheet metal. These mechanical fasteners combine ease of installation, high strength, and permanent attachment, making them indispensable in sectors such as electronics, telecommunications, automotive, and aerospace.
This article provides a comprehensive overview of pressure rivet screws, covering their design principles, working mechanisms, material options, performance benefits, installation techniques, and major application scenarios.
1. Design and Structure
A pressure rivet screw is designed to provide strong threads in thin sheet metal where traditional threading is impractical. Its typical structural features include:
-
Head: Often flat or hexagonal, depending on whether the screw should be flush-mounted or externally driven.
-
Threaded Shaft: Allows standard machine screws or bolts to be fastened to it once installed.
-
Knurled Shank or Clinch Feature: A critical section designed to deform and cold-form the surrounding metal during installation, locking the screw in place permanently.
Some designs include a slight undercut or groove beneath the head to further enhance the grip within the metal substrate. Others incorporate serrations to resist torque or loosening under vibration.
2. Installation Mechanism
Pressure rivet screws are installed using a cold-forming process that utilizes force rather than heat. The procedure includes:
-
Hole Preparation: A precise hole is punched or drilled into the sheet metal. The hole diameter and sheet thickness must match the screw’s design specifications.
-
Alignment: The screw is inserted into the hole, with the clinch feature positioned within the sheet.
-
Application of Axial Force: A press (manual, hydraulic, or pneumatic) applies force to seat the screw. As pressure is applied, the sheet material plastically deforms around the knurled or grooved section.
-
Interlocking Engagement: The displaced metal fills into the recess or groove, forming a mechanical interlock that prevents both axial movement and rotation.
This installation does not remove material from the sheet, preserving structural integrity while forming robust and permanent threads.
3. Material Options
The choice of material for pressure rivet screws depends on several factors, including mechanical strength, environmental exposure, compatibility with the base material, and cost considerations. Common materials include:
-
Carbon Steel: Offers high tensile strength and cost-efficiency. Often used in general-purpose applications.
-
Stainless Steel: Provides excellent corrosion resistance and is suitable for harsh or outdoor environments. Common grades include A2 (304) and A4 (316).
-
Aluminum Alloy: Lightweight and corrosion-resistant; often used in aerospace or electronic enclosures.
-
Brass: Selected for electrical conductivity and resistance to corrosion in specific applications like electrical panels.
Surface treatments further enhance performance:
-
Zinc Plating: Adds corrosion resistance for steel components.
-
Passivation: Improves corrosion resistance in stainless steel fasteners.
-
Black Oxide: Used for aesthetic and anti-corrosion purposes.
-
Nickel Plating: Applied to brass or copper-based fasteners for improved wear and corrosion protection.
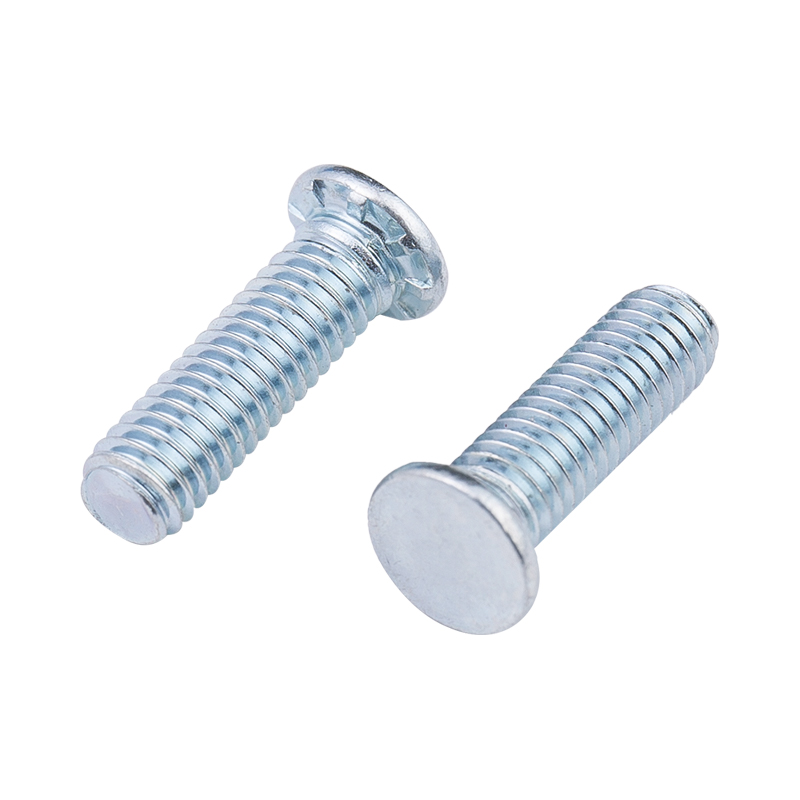
4. Performance Advantages
Pressure rivet screws offer numerous advantages over conventional fastening systems, especially in sheet metal applications:
-
Permanent Fixation: Once installed, they cannot loosen or rotate under operational stresses, eliminating the need for periodic tightening or inspection.
-
Strong Load-Bearing Threads: They provide durable, reusable threads even in metal sheets as thin as 0.5 mm.
-
No Thermal Damage: The cold-press method avoids the metallurgical changes and potential warping associated with welding or brazing.
-
Clean and Precise Assembly: Ideal for cleanroom or electronics applications where minimal debris or contamination is allowed.
-
Reduced Assembly Time: Compatible with automated systems and robotic press equipment, enabling fast, consistent production.
-
Compact Footprint: Provide strong fastening without requiring nuts, tapped holes, or additional parts.
5. Engineering Considerations
Successful use of pressure rivet screws depends on proper engineering and installation:
-
Sheet Material Ductility: The base sheet must be ductile enough to allow plastic deformation during installation. Hard or brittle materials (e.g., high-carbon steel, hardened aluminum) may crack or fail.
-
Correct Hole Sizing: Tolerances must be precise to allow secure seating without excessive clearance.
-
Sheet Thickness Compatibility: Each screw design is optimized for a specific thickness range. Using the wrong match can lead to insufficient anchoring or sheet rupture.
-
Axial Force Application: Uniform, controlled pressure must be applied to achieve proper seating and metal flow.
-
Thread Engagement Depth: Design engineers should consider how much thread engagement is required for the mating screw to ensure reliable load distribution.
6. Variants and Customization
There are various types of pressure rivet screws tailored for different applications:
-
Flush-head Types: Designed to sit level with the panel surface, ideal for enclosures or assemblies with limited clearance.
-
Stud Types: Provide a projecting threaded post for components that require stacking or spacing.
-
Standoff Types: Combine internal and external threading, often used in printed circuit board (PCB) mounting.
-
Self-locking Screws: Feature pre-applied locking compounds or nylon patches to resist vibration-induced loosening.
Manufacturers also offer customization options, including:
-
Metric and imperial thread standards
-
Special head geometries
-
Non-magnetic or high-temperature materials
-
Color-coded finishes for easy identification
7. Application Scenarios
Pressure rivet screws are used across a broad spectrum of industries due to their versatility and strength.
Electronics and Telecommunications
In compact electronic devices, components must be secured to thin chassis or casings without compromising space or heat management. Pressure rivet screws provide reliable threads in aluminum or steel housings while maintaining thermal and EMI integrity.
Automotive Engineering
Automobile interiors and electronic modules often use these fasteners to mount circuit boards, control panels, and trim components. Their vibration resistance is particularly valuable in dynamic environments.
Aerospace and Defense
Weight-saving and structural reliability are crucial. Pressure rivet screws offer both, with stainless steel or titanium variants used in aircraft panels, avionics, and defense equipment.
Industrial Control Systems
Control cabinets and electrical distribution boxes rely on these fasteners for mounting DIN rails, grounding terminals, and external brackets.
Home Appliances and HVAC
From air conditioners to washing machines, pressure rivet screws simplify the assembly of panels and housings made from thin metal sheets.
8. Installation Equipment and Automation
In large-scale manufacturing, installation is performed using pneumatic or hydraulic presses fitted with special anvils or fixtures. Some advanced lines feature CNC-controlled robotic arms capable of high-precision positioning and insertion, increasing throughput while reducing human error.
Automated systems often include force sensors and visual inspection systems to detect misalignment or incomplete seating. This ensures consistent performance and quality control in high-volume production.